In the world of manufacturing and construction, understanding the diverse types of wholesale thread rolling is crucial. It is important not only from a practical standpoint but also to enhance cost efficiency and maintain high-quality standards across various applications. This process, an essential element in industrial machining, provides the strength and resilience required in metalworking. This article delves into the nuances of thread rolling and explains why it holds an esteemed position in various industries, from automotive to aerospace.
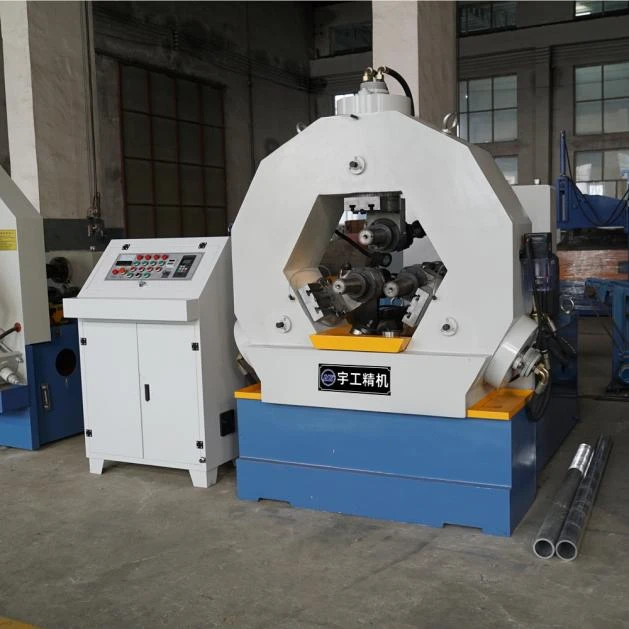
Thread rolling stands apart from cutting processes due to how it forges the threads onto workpieces. Instead of removing material, thread rolling reshapes it, resulting in a denser and more durable product. This process ensures threads that can withstand higher tension, an aspect particularly beneficial in heavy-duty industries. The efficiency and eco-friendliness of thread rolling deserve attention because the technique eliminates waste, keeping operations sustainable while also reducing production costs.
Various types of thread rolling processes exist to cater to different manufacturing needs. Each method comes with its own set of advantages, suited to particular applications
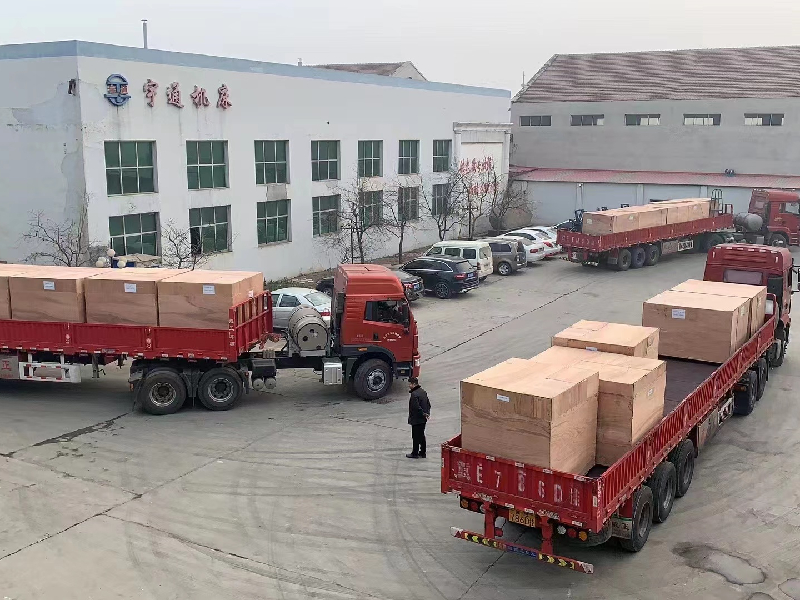
1. Flat Die Thread Rolling This method involves two flat dies placed parallel to each other. The workpiece rolls between them, forming threads as they imprint patterns onto the surface. Flat die threading is preferred for its speed and ability to produce highly accurate threads. Its design simplicity makes it favored for small and medium-sized productions.
2. Planetary Die Thread Rolling Ideal for continuous operations, this type utilizes a single die that rotates around the workpiece. The process is perfect for small thread rolls and excels in rapid production environments, adding minimal stress to the materials, which helps maintain their intrinsic qualities.
3. Two-Die Thread Rolling Also known as radial die threading, this process uses two cylindrical dies that press the threads onto the workpiece. It’s effective for large-scale production and particularly adept at creating precision threads thanks to its robust mechanism.
wholesale types of thread rolling
4. Helical Thread Rolling Employed for creating helical threads, this process is performed using helical rolls. This method is valuable for producing fasteners and other specific threaded elements, allowing for high consistency throughout the operation.
Choosing the right thread rolling solution depends significantly on the materials in use and the desired strength and durability of the final product. Experienced manufacturers understand the subtleties associated with each method and make choices based on specific project requirements, relying on their established expertise.
Industries worldwide place trust in thread rolling processes due to their inherent advantages over other methods of thread production. Not only do these processes produce superior results, but they reflect an organization’s commitment to quality and sustainability. With materials spared from the wastage typically associated with cutting methods, businesses are paving the way for greener manufacturing processes.
Moreover, the authority of thread rolling in the domain of manufacturing cannot be overstated. With its ability to increase tensile strength and fatigue resistance, this process produces components that play pivotal roles in safety-critical applications. The aerospace and automotive sectors, in particular, leverage the benefits of thread rolling to produce components that meet rigorous safety standards. Engineers and project managers in these industries rely on the integrity of thread-rolled components to ensure that each part performs its function under demanding conditions.
Trustworthiness in the product is a result of meticulous manufacturing standards and adherence to stringent testing protocols. Through the years, thread rolling has consistently demonstrated reliability, forming the backbone of various industrial applications. Industries that rely on high-strength fasteners and connectors can ill-afford the slightest compromise in reliability, making thread rolling an irreplaceable part of their production lines.
In the ever-evolving landscape of manufacturing, thread rolling continues to stand the test of time due to its exceptional combination of efficiency, reliability, and sustainability. By understanding the various types of thread rolling and strategically applying this knowledge, industries can ensure the most robust and economically efficient solutions are utilized, paving the way for continued innovation and growth.