Thread rolling machines are the heart of precision engineering in manufacturing, particularly in the fastener and automotive industries. OEMs, or Original Equipment Manufacturers, are pioneering this domain with cutting-edge technologies and diverse types designed to meet varied industrial needs. Understanding these machines' different types enhances operational efficiency, product quality, and competitive advantage.

OEMs have revolutionized thread rolling technology by introducing several types of machines, each with unique attributes tailored for specific tasks.
Flat die thread rolling machines are known for their versatility and simplicity. They are ideally suited for mass production scenarios where consistency and speed are paramount. The flat dies press the metal stock between two flat plates, achieving rapid, precise, and repeatable threads, making it an industry favorite for high-volume production.
Cylindrical or round die thread rolling machines represent a leap forward in precision engineering. These machines are instrumental when it comes to generating intricate and high-strength threads. Utilizing round dies, the process involves workpieces being rotated and pressed against rolling dies, ensuring uniformity and superior mechanical properties in the finished product. This makes them indispensable in manufacturing critical components for automotive and aerospace sectors, where thread integrity is non-negotiable.
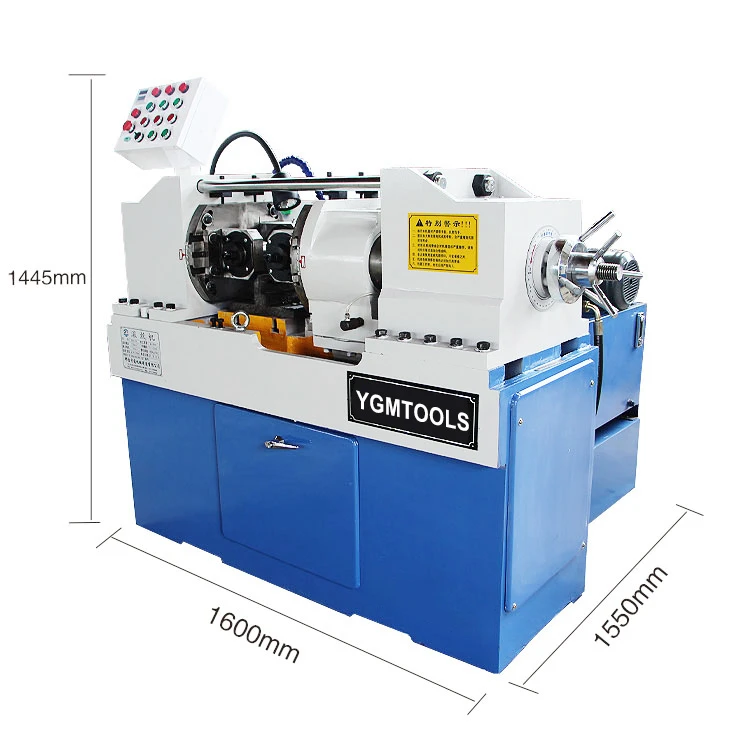
Planetary thread rolling machines offer another realm of possibilities with their unique construction geared towards handling larger diameters and longer screw threads. These machines employ a combination of rotating dies that move in orbital patterns, a method which ensures the application of uniform pressure across the workpiece. As a result, they are particularly effective for manufacturing substantial parts used in heavy machinery and infrastructure projects, balancing strength and durability.
Beyond the basic configurations of flat and round dies, innovative OEMs are exploring hydraulic thread rolling machines. These are particularly transformative for industries requiring adaptable and precise operations under varying pressure conditions. The hydraulic mechanism allows for precise control of pressure application, enabling manufacturers to customize thread rolling processes according to material properties and desired thread characteristics. Such machines exemplify the sophistication and adaptability of modern thread rolling technology.
Further extending the capabilities of traditional thread rolling machines, CNC-equipped models introduce unparalleled automation and precision. CNC, or Computer Numerical Control, allows for pre-programmed, precise control over the threading process. CNC machines offer the benefits of reduced human error, increased production speed, and the ability to produce complex threading patterns consistently. These features are especially crucial in today's competitive markets, where precision and efficiency are key differentiators.
oem types of thread rolling machine
OEMs in this field also innovate by incorporating multifunctional thread rolling machines that combine various operations such as chamfering, knurling, and rolling in a single setup. These machines not only reduce cycle times but also diminish the need for multiple setups, reducing labor costs and material handling time. This integration is quintessential for industries looking to streamline processes while maintaining high standards of precision and quality.
In addition to technological diversity, the environmental considerations are gaining attention, with OEMs designing machines that are energy-efficient and produce minimal material waste. Sustainability is becoming an integral part of the engineering process, reflecting industry trends towards eco-friendly practices. By prioritizing sustainability, OEMs not only contribute to global conservation efforts but also appeal to environmentally conscious consumers and partners.
Selecting the appropriate thread rolling machine type is crucial for maximizing operational output and quality. It involves careful analysis of production requirements, material characteristics, and desired thread specifications. Consulting with seasoned industry professionals and leveraging OEM expertise are vital steps to ensure optimal machine selection and integration into manufacturing processes.
To maintain competitive edge and consumer trust, OEMs are steadfast in their commitment to advancing thread rolling technology. By investing in research and development, continually improving machine capabilities, and fostering a deep understanding of industry needs, these manufacturers ensure they remain at the forefront of global manufacturing technologies.
Collectively, OEM types of thread rolling machines demonstrate a blend of traditional engineering excellence intertwined with modern technological advancements. These machines not only meet but often exceed the rigorous demands of contemporary manufacturing, epitomizing quality, innovation, and sustainable growth in the world of industrial machinery.