The realm of OEM thread rolling machines represents a pinnacle of precision engineering and plays a crucial role in manufacturing facilities around the globe. Setting up an OEM thread rolling machine effectively requires not only a technical understanding but also a keen awareness of the variables that influence production quality and efficiency.
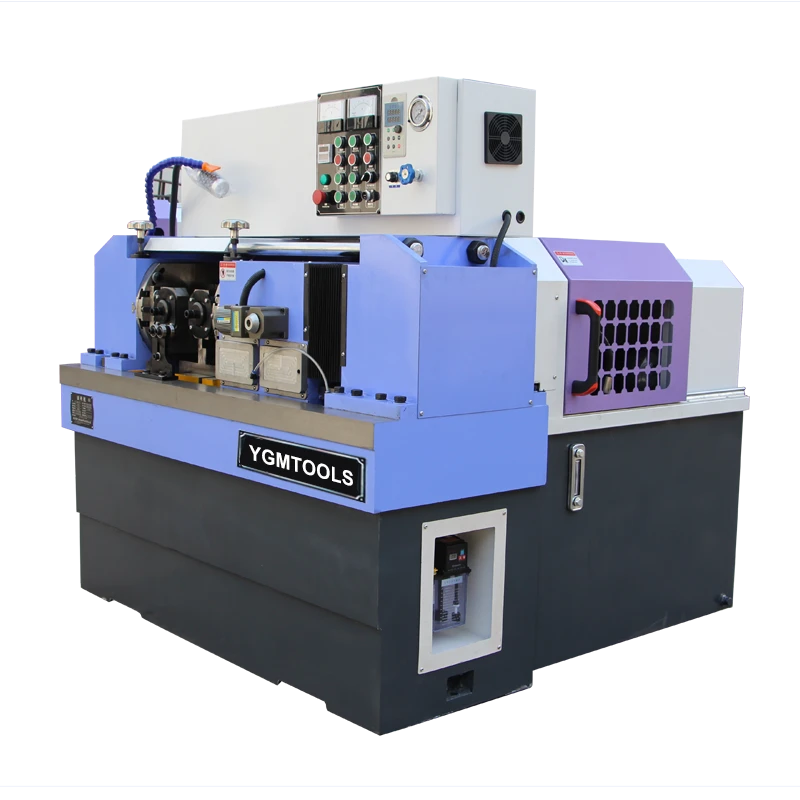
Thread rolling is a cold-forming process that produces precision threads by pressing a die against a rotating cylindrical workpiece. This method, unlike cutting, does not remove material but instead displaces it, enhancing the part's strength and surface finish. Consequently, understanding the specificity and setup of these machines is paramount to leveraging their full potential.
The initial step in setting up an OEM thread rolling machine involves selecting the appropriate model that aligns with the intended application. Machines vary significantly based on capabilities, such as the type of threads produced, diameters, and materials they can handle. Key considerations include the range of thread sizes, the type of threads (metric, imperial, or special profiles), and the production volume.
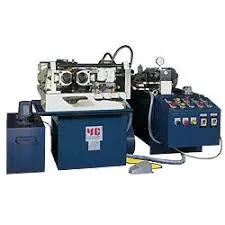
Once you have chosen the right machine, a comprehensive examination of the manufacturer's guidelines is essential. These manuals offer insights into machine specifications, setup instructions, and maintenance schedules. An in-depth understanding of these documents will ensure that setup and operational parameters align with the OEM standards, guaranteeing both machine longevity and product quality.
The physical setup demands meticulous attention to detail. First, ensure that the machine is securely anchored to prevent vibrations that could affect thread accuracy. The workspace should be organized to facilitate ease of access for operators and maintenance personnel. Proper alignment and calibration are critical; even slight misalignments can lead to defective threads and increased material waste. Utilize precision measuring tools to verify that all components are correctly positioned.
Selecting the appropriate dies is another crucial setup aspect. Dies must be chosen based on the material and diameter of the workpiece, as well as the desired thread profile. Quality dies are essential for producing consistent results and should be regularly inspected for wear and tear. The dies’ lifespan can significantly impact the machine’s overall efficiency and the quality of the threads produced.
Considering the materials is also vital. Different materials react distinctively to the pressures exerted during the rolling process. For instance, softer metals may require a slower speed to prevent deformation, while harder materials might demand more robust equipment and additional lubrication to avoid overheating and tool wear.
oem thread rolling machine setup
Moreover, effective lubrication is fundamental in preserving both the machine and the products' integrity. Lubricants reduce friction, dissipate heat, and facilitate smoother operation. The selection of lubricant should correspond with the material type and rolling speed, ensuring optimal operational conditions and prolonging the dies' lifespan.
Monitoring and quality control should be an ongoing process post-setup. Real-time monitoring systems can be integrated to provide data on machine performance, enabling operators to make timely adjustments. These systems can detect anomalies such as fluctuating speeds or abnormal pressures, often indicating potential issues before they result in significant downtime or product defects.
Training is vital to maximize the machine's effectiveness and lifespan. Machine operators should receive comprehensive training covering the machine's intricacies, setup procedures, safety protocols, and troubleshooting techniques. A well-informed operator is indispensable for maintaining machine efficiency and ensuring high-quality output.
In environments where OEM thread rolling machines are essential, adherence to preventive maintenance schedules cannot be overemphasized. Regular inspections and maintenance prolong the machine's operational life and prevent unexpected breakdowns. Parts such as bearings, gears, and lubrication systems should be routinely checked and serviced to maintain optimal performance.
Trustworthiness in producing high-quality threads with an OEM thread rolling machine stems from a blend of the right machinery choice, meticulous setup, qualified personnel, and a commitment to ongoing maintenance and monitoring. Only by harmonizing these elements can manufacturers ensure the production of robust, precision threads that meet industry standards and customer expectations.
Ultimately, the efficacy of an OEM thread rolling machine setup lies in the integration of experience, expertise, authority, and trustworthiness. By adhering to these principles, manufacturers can enhance their production processes, reduce waste, and deliver products that stand out in an ever-competitive market.