The Pivotal Role of Bolt Rolling Machines in Modern Industry
In the realm of engineering and manufacturing, one piece of machinery that plays an indispensable role is the bolt rolling machine. This specialized equipment is designed to shape and form bolts, screws, and other threaded fasteners with precision and efficiency, significantly contributing to the streamline of production processes.
A bolt rolling machine, often referred to as a thread rolling machine, operates on a principle that involves the application of compressive force to deform metal into the desired thread pattern. Unlike cutting or machining methods, rolling creates threads by shaping the metal rather than removing it, resulting in a stronger, more durable product with a superior surface finish. The process is also known for its energy efficiency and reduced waste, making it an environmentally friendly option.
The design of a bolt rolling machine typically consists of three main components the power source, the forming dies, and the workpiece holder. The power source, usually an electric motor, supplies the necessary torque to rotate the dies. These dies, made from high-strength steel, are precisely machined to replicate the thread profile. The workpiece holder secures the bolt or screw blank in place, ensuring accurate alignment during the rolling process.
The operation of a bolt rolling machine is both precise and swift. The blank is clamped between the dies, which then rotate, applying pressure to form the threads The blank is clamped between the dies, which then rotate, applying pressure to form the threads
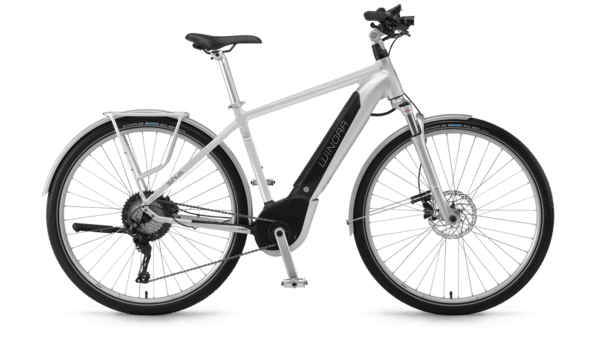
The blank is clamped between the dies, which then rotate, applying pressure to form the threads The blank is clamped between the dies, which then rotate, applying pressure to form the threads
bolt rolling machine. As the dies move over the metal, the material flows under pressure, creating the thread without generating heat or leaving burrs. This cold-forming process not only enhances the mechanical properties of the fastener but also allows for the creation of complex thread geometries that might be challenging or impossible to achieve through other methods.
Bolt rolling machines find their utility across a broad spectrum of industries, from automotive and aerospace to construction and machinery manufacturing. They are instrumental in mass-producing high-quality bolts and screws, ensuring consistency and reliability in the final products. Moreover, the ability to customize thread specifications makes these machines adaptable to diverse engineering requirements.
In conclusion, the bolt rolling machine is a testament to the fusion of technological innovation and practical engineering. It has revolutionized the production of threaded fasteners, boosting productivity, reducing costs, and improving the overall quality of the end product. As technology continues to evolve, we can expect even more advanced bolt rolling machines that will further refine this process, pushing the boundaries of manufacturing efficiency and precision.