The Precision Craftsmanship of Mini Thread Rolling Machines
In the world of industrial machinery, a mini thread rolling machine holds a unique position due to its versatility and precision. This compact marvel is an engineering masterpiece that revolutionizes the manufacturing process, particularly in the production of threads on various materials.
Thread rolling is a cold-forming process that creates threads by applying pressure on a workpiece with a pair of precisely engineered dies. Unlike cutting methods, which remove material, thread rolling deforms the surface to create strong, high-quality threads. Mini thread rolling machines bring this capability into a compact, manageable form, ideal for small-scale operations or tasks requiring intricate detailing.
These machines, despite their miniature size, pack a powerful punch. They are equipped with robust motors and advanced control systems, enabling them to handle a wide range of materials, from soft metals like aluminum to hard steels. The miniaturization does not compromise their efficiency; instead, it enhances maneuverability and accessibility, making them suitable for confined spaces and intricate designs.
One of the key advantages of mini thread rolling machines lies in their precision. The dies used in these machines are meticulously designed to ensure accurate thread dimensions, pitch, and form. The process results in threads with superior surface finish, high fatigue strength, and excellent tolerance control. This makes them particularly valuable in applications where reliability and durability are paramount, such as aerospace, automotive, and precision engineering industries.
Moreover, mini thread rolling machines offer a cost-effective solution due to their low energy consumption and reduced waste generation
Moreover, mini thread rolling machines offer a cost-effective solution due to their low energy consumption and reduced waste generation
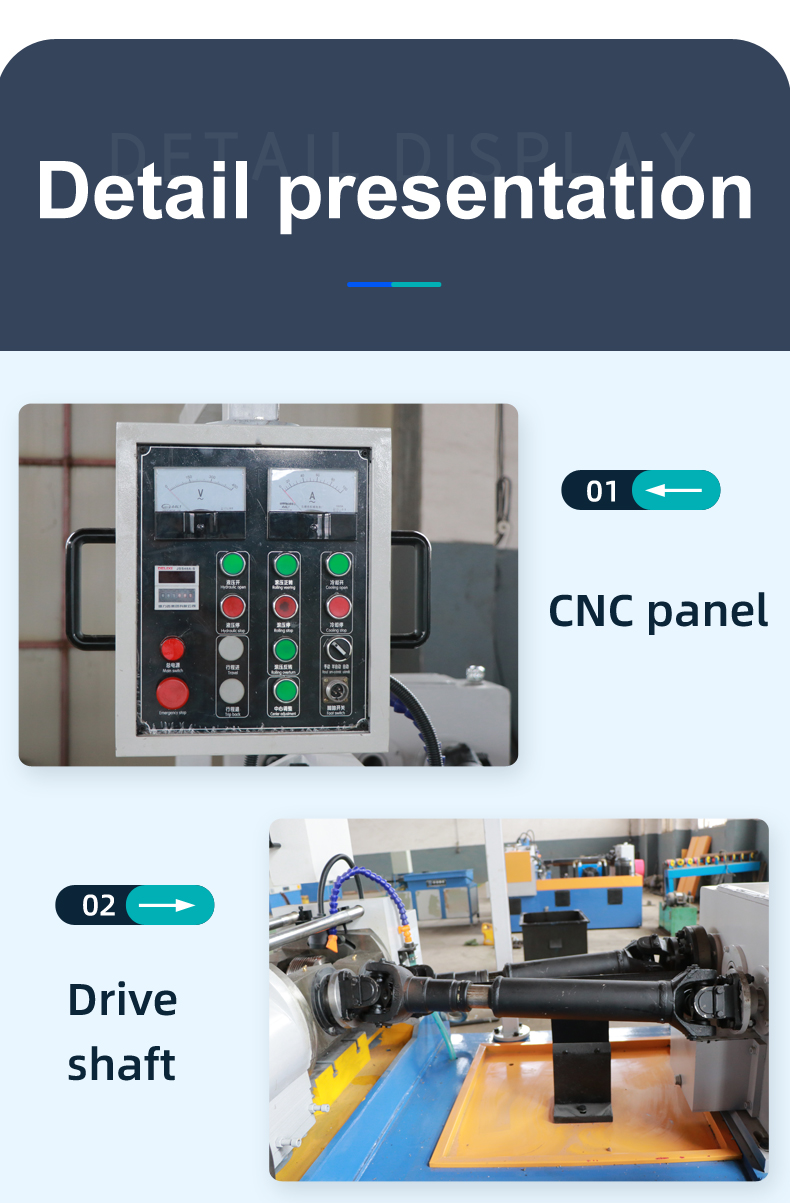
Moreover, mini thread rolling machines offer a cost-effective solution due to their low energy consumption and reduced waste generation
Moreover, mini thread rolling machines offer a cost-effective solution due to their low energy consumption and reduced waste generation
mini thread rolling machine. The process is relatively faster than traditional tapping or threading methods, increasing productivity without escalating operational costs. Additionally, the machines' durability and low maintenance requirements contribute significantly to their overall cost-effectiveness.
The mini thread rolling machines also foster flexibility in production. They can be easily integrated into automated production lines or operated manually, catering to diverse manufacturing needs. Their user-friendly interface and programmable controls allow for quick adjustments and customization, accommodating various thread specifications.
Innovations in technology have further enhanced the capabilities of mini thread rolling machines. Today, they come equipped with advanced features such as digital displays, programmable logic controllers (PLCs), and real-time monitoring systems, allowing for precise process control and data analysis.
In conclusion, the mini thread rolling machine is a testament to the ingenuity of modern engineering. Its compact design, precision, efficiency, and versatility make it an indispensable tool in numerous industries. As manufacturing continues to evolve, these machines will undoubtedly play a pivotal role in shaping the future of thread production, ensuring quality, strength, and precision in every thread they produce.