Navigating the world of OEM flat die thread rolling machines involves understanding the critical components that set these machines apart in the manufacturing industry. Known for their precision and efficiency, these machines play a pivotal role in automotive, aerospace, and hardware sectors. My experience with these machines has provided insights into their superior functionality, industry applications, and the significant advantages they offer over traditional threading methods.
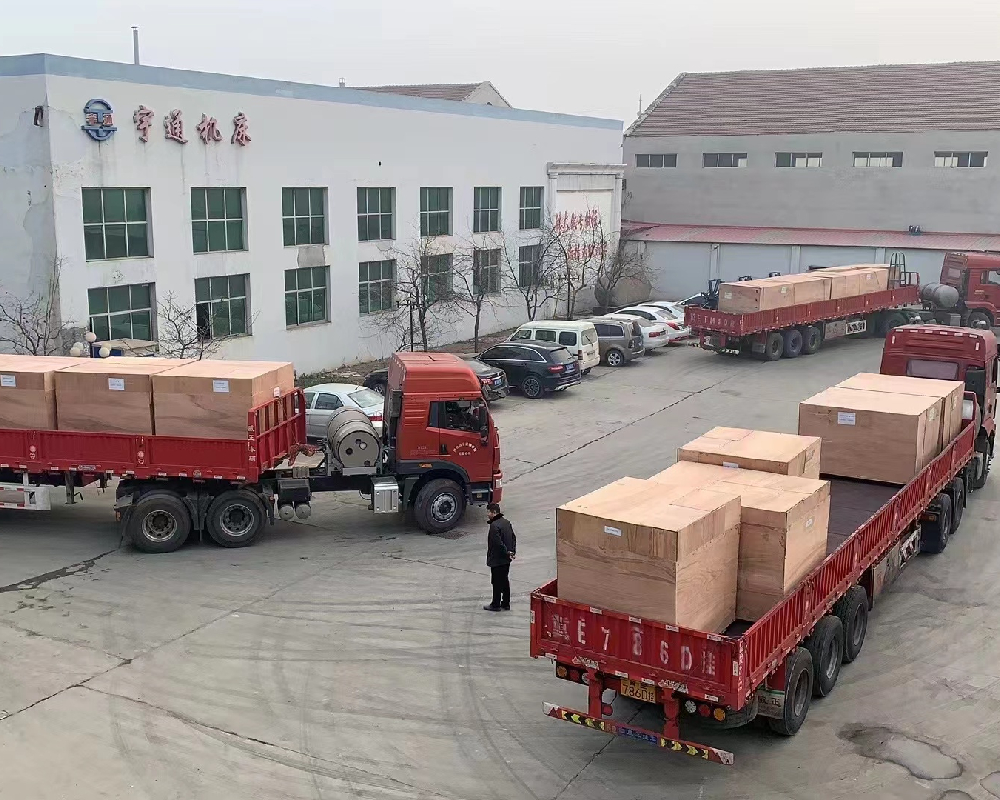
Flat die thread rolling machines operate on the principle of cold forming, a process that involves deforming materials at ambient temperatures. This method not only enhances material properties but also maintains structural integrity and produces impeccable, consistent threads. The machines utilize two flat dies, one stationary and the other reciprocating, to form threads through a high-efficiency rolling action. This seamless process is designed to meet high production demands, making it an asset in high-volume manufacturing settings.
Expertise in operating these machines is crucial. It begins with an understanding of the machine's architecture—comprising a sturdy frame, sophisticated control systems, and precise die settings. When paired with the right tooling, these machines can achieve remarkable levels of accuracy and repeatability. As an expert in the field, I've witnessed how crucial it is to calibrate dies correctly; even minor misalignments can impact thread quality significantly.
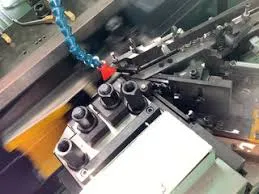
The authoritativeness of OEM flat die thread rolling machines can be attributed to their versatility and adaptability. They cater to various materials, including metals and alloys, allowing for customization based on specific industry requirements. For instance, in the automotive industry, these machines are vital for producing threaded components that require superior fatigue resistance—a critical factor for safety and durability.
oem flat die thread rolling machine
Trust in these machines comes from their ability to deliver high-strength threads without the need for additional heat treating, which is often required in conventional threading. The material's grain structure is altered in a way that enhances tensile strength and prolongs the lifespan of the components. This aspect not only translates into cost savings in the manufacturing process but also assures clients of the durability and reliability of their products.
Several case studies within the aerospace industry highlight the use of OEM flat die thread rolling machines in producing parts that comply with stringent aeronautical standards. The consistency in thread pitch and depth is crucial for aerospace components, where even the slightest deviation can lead to catastrophic failures. These machines have proven their worth by delivering components that meet these exacting standards while excluding the variations possible in traditional machining.
Furthermore, the adaptability of these machines extends to incorporating the latest technological innovations. Modern flat die thread rolling machines are equipped with advanced computer numerical control (CNC) systems, which enhance precision and allow for meticulous adjustments tailored to specific tasks. This feature not only increases productivity but also reduces downtimes associated with human error.
In conclusion, OEM flat die thread rolling machines stand as a testament to the evolution of manufacturing technology. Their unparalleled efficiency, coupled with the ability to produce high-quality threads consistently, renders them a preferred choice in sectors that demand precision and reliability. Mastery of these intricate machines and keeping abreast of technological advancements contribute significantly to maintaining a competitive edge in the manufacturing domain, thus ensuring the production of components that meet and exceed industry standards.