Custom Types of Thread Rolling An In-Depth Perspective
Thread rolling, an essential process in metalworking, is a cold-forming operation that creates threads on a part by shaping it with a die. This method is preferred over cutting due to its ability to produce stronger, more precise threads with a higher surface finish. However, the versatility of thread rolling extends beyond standard applications, as it can be tailored to accommodate a wide range of custom types for specific industrial needs.
Custom thread rolling is a specialized process that allows manufacturers to create unique thread profiles, pitches, and sizes that meet unconventional design requirements. It opens up new possibilities in industries such as aerospace, automotive, and oil and gas, where precision and durability are paramount.
One significant advantage of custom thread rolling is the capacity to work with diverse materials. From soft aluminum to hard stainless steel, the process can adapt to the unique properties of each material, ensuring optimal thread integrity and performance. Furthermore, custom thread rolling can also accommodate irregular or complex geometries, such as internal threads in blind holes or external threads on contoured surfaces.
There are three primary types of thread rolling processes single-die, double-die, and three-die rolling. Each offers distinct advantages and can be customized further to suit specific applications. For instance, single-die rolling is ideal for producing small batches of unique thread designs, while double-die and three-die methods are more efficient for mass production of complex or large-sized threads For instance, single-die rolling is ideal for producing small batches of unique thread designs, while double-die and three-die methods are more efficient for mass production of complex or large-sized threads
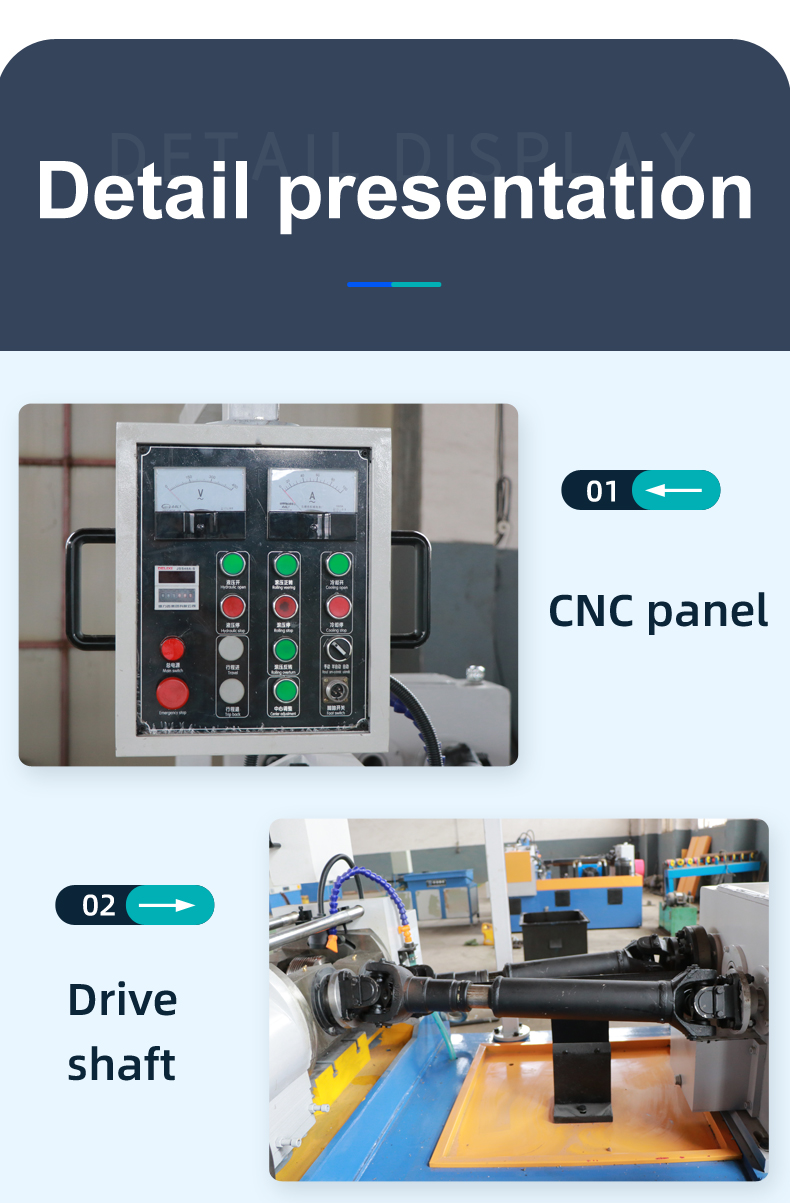
For instance, single-die rolling is ideal for producing small batches of unique thread designs, while double-die and three-die methods are more efficient for mass production of complex or large-sized threads For instance, single-die rolling is ideal for producing small batches of unique thread designs, while double-die and three-die methods are more efficient for mass production of complex or large-sized threads
custom types of thread rolling.
In addition to the type of rolling, the dies used in custom thread rolling can be intricately designed to achieve intricate thread patterns. These dies can be made from high-speed steel, carbide, or even ceramic, depending on the required durability and the material being rolled.
Custom thread rolling also offers benefits in terms of efficiency and cost-effectiveness. By creating threads without generating chips or sparks, it reduces waste and eliminates the need for post-processing, such as cleaning or coating. Moreover, the process can be automated, leading to increased productivity and consistent quality.
In conclusion, custom types of thread rolling open up a world of possibilities in engineering and manufacturing. It empowers designers to push the boundaries of thread design, enabling the creation of components with enhanced performance, durability, and functionality. Whether it's for a specialized fastener in aerospace or a unique threading solution in the automotive industry, custom thread rolling continues to play a pivotal role in driving innovation and meeting the ever-evolving demands of modern engineering.